Oferta test MW
Filtry pulsacyjne workowe
Przeznaczenie filtrów workowych
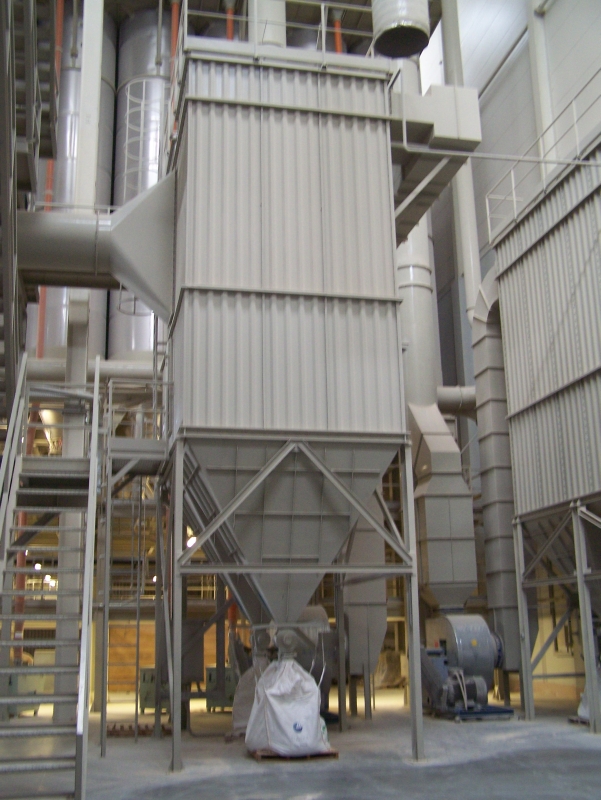
Filtry workowe przeznaczone są do odpylania powietrza z pyłów suchych i nie klejących. Nie mogą być stosowane w wersji normalnej dla pyłów wybuchowych, ponieważ nie posiadają odpowiednich zabezpieczeń. Dla mieszanin pyłowo-powietrznych wybuchowych filtry wykonywane są zgodnie z wymaganiami ATEX i posiadają zabezpieczenia odpowiednie dla danego pyłu, takie jak:
- uziemienie worków filtracyjnych wykonanych z odpowiedniej włókniny elektroprzewodzącej,
- otwory dekompresyjne zamknięte klapą lub atestowaną membraną dekompresyjną.
Filtry przeznaczone są zasadniczo do pracy w części podciśnieniowej instalacji, ale mogą także pracować w części nadciśnieniowej.
Filtry pulsacyjne workowe mogą być stosowane w instalacjach odpylających w przemyśle cementowym, wapienniczym, odlewniczym, hutniczym, materiałów drogowych i budowlanych, chemicznym, w kotłowniach, instalacjach odsiarczania, itp.
Budowa i działanie filtrów workowych
Filtry pulsacyjne workowe składają się z następujących głównych podzespołów:
- komora oczyszczonego powietrza
- komora filtracyjna,
- zespół worków filtracyjnych z koszami,
- zsyp (pojedynczy lub podwójny) z przenośnikiem ślimakowym i dozownikiem celkowym,
- konstrukcja wsporcza,
- instalacja elektryczna z szafką sterowniczą.
Komora oczyszczonego powietrza ma kształt prostopadłościanu. Komora od góry zamknięta jest otwieranymi pokrywami. W ścianie bocznej posiada otwór wylotowy czystego powietrza. Komora wyposażona jest w rurki przedmuchowe, kolektor sprężonego powietrza oraz zawory elektromagnetyczne. Kolektor sprężonego powietrza magazynuje odwodnione i odolejone powietrze przeznaczone do regeneracji worków. Przepływ sprężonego powietrza do regeneracji odbywa się z kolektora poprzez zawory elektromagnetyczne, rurki przedmuchowe i dysze zamontowane w koszach filtracyjnych.
Komora filtracyjna ma kształt prostopadłościanu. W komorze filtracyjnej znajdują się drzwi włazowe umożliwiające montaż i demontaż koszy z workami filtracyjnymi. Wewnątrz komory zainstalowane są kosze z workami filtracyjnymi. Są one osłonięte od wlotu rzędem osłon. W ścianie komory filtracyjnej znajduje się otwór wlotowy zanieczyszczonego powietrza.
Zespół worków filtracyjnych z koszami jest umocowany w blasze sitowej pomiędzy komorą oczyszczonego powietrza a komorą filtracyjną. W otworach blachy sitowej przy pomocy pierścieni rozprężnych worków filtracyjnych zamocowane są worki filtracyjne. Do wnętrza worków włożone są kosze filtracyjne wyposażone w dysze Venturiego. Dysze wykonane są z polipropylenu lub aluminium.
Zsyp ma kształt ostrosłupa, graniastosłupa. Może być pojedynczy lub podwójny. Zsyp zakończony jest przenośnikiem ślimakowym i dozownikiem celkowym. Służą one do szczelnego zamknięcia filtra od strony zsypu oraz do usuwania odpadającego pyłu.
Konstrukcja wsporcza składa się z ramy, na której zamontowany jest filtr oraz podpór. Filtr może być wyposażony w drabinę i barierki na górze filtra
Instalacja elektryczna składa się z szafki sterowniczej oraz przewodów łączących szafkę z zaworami elektromagnetycznymi dla regeneracji worków filtracyjnych.
Filtry pulsacyjne workowe przewidziane są do instalowania w pomieszczeniach zamkniętych i na otwartej przestrzeni. Jeżeli odpylane gazy nie zawierają pary wodnej, filtry te mogą być instalowane na otwartej przestrzeni bez izolacji termicznej. Filtry mają budowę modułową. Wykonywane i transportowane są w elementach. Montowane są poprzez skręcanie śrubami i doszczelnienie połączeń pastami, głównie silikonem. Położenie wlotu i wylotów gazu, wysypu pyłu i doprowadzenie sprężonego powietrza mogą być zmienione o 180o.
W zależności od temperatury oczyszczanego powietrza filtry wyposażone są w dysze polipropylenowe (do 60 C) lub aluminiowe (powyżej 60 C). Dla każdej instalacji odpylającej wymagany jest osobny dobór rodzaju i struktury włókniny filtracyjnej (filcu igłowego) oraz parametrów filtracji i regeneracji. Dobór ten należy przeprowadzić
w zależności od temperatury zapylonego powietrza, rodzaju i właściwości pyłu, zawartości pary wodnej, substancji kwasowych i zasadowych. Worki mogą być wykonane z różnych rodzajów filcu igłowanego (poliester, polipropylen, Dolomit, PPS, Nomex, P-84, Teflon, itd.) i z różnymi rodzajami obróbek. Doboru tego dokonuje inwestor lub projektant instalacji odpylającej. Producent filtrów udziela porad w doborze włókniny i parametrów filtracji i regeneracji. Kosze mogą być jednoelementowe lub dzielone, wykonane ze stali węglowej i pomalowane lub ze stali kwasoodpornej. Na życzenie zamawiającego mogą być wprowadzone zmiany i dodatkowe wyposażenie
Filtry zazwyczaj są wykonane w wersji wymiany worków od góry. Tzn. od strony czystej. Po otwarciu pokrywy na komorze oczyszczonego powietrza i zdjęciu rurki przedmuchowej można wyjąć kosz, a następnie worek filtracyjny. Worki filtracyjne mocowane są w blasze sitowej za pomocą wszytych w nie pierścieni rozprężnych, tzw. „snapringów”. Umożliwia to szybką wymianę worków
Zanieczyszczone powietrze doprowadzone jest do komory rozprężnej w komorze filtracyjnej. Następnie zanieczyszczone powietrze przechodzi przez worki filtracyjne. Pył zatrzymuje się na zewnętrznej powierzchni worków. Oczyszczone powietrze przechodzi przez worki filtracyjne do komory oczyszczonego powietrza, skąd odprowadzone jest na zewnątrz filtra. W miarę upływu czasu rośnie grubość warstwy pyłu na powierzchni worków. Usuwanie pyłu z worków realizowane jest poprzez impulsy sprężonego powietrza kierowane do każdego z worków. Impuls sprężonego powietrza jest wytwarzany przez zawór elektromagnetyczny sterowany z szafki sterowniczej. Zawór otwiera się na bardzo krótki czas i sprężone powietrze z kolektora wpada w postaci impulsu do rurek przedmuchowych, z których poprzez otwory umieszczone nad każdym workiem, dostaje się do dysz Venturiego. Powstały impuls sprężonego powietrza jest wzmocniony w dyszy i przesuwa się jako fala powietrzna wzdłuż worka powodując jego wybrzuszenie i odpadnięcie pyłu. Pył spada do zsypu, skąd za pomocą przenośnika ślimakowego i dozownika celkowego usuwany jest na zewnątrz filtra.
Pracą regeneracji worków filtracyjnych filtrów pulsacyjnych sterują następujące rodzaje szafek sterowniczych
- ze sterowaniem czasowym, w którym ustala się czas trwania impulsu oraz częstotliwość regeneracji
- ze sterowaniem ∆p, w których regeneracja worków filtracyjnych uzależniona jest od oporów przepływu powietrza przez worki filtracyjne.
Regeneracja worków filtracyjnych odbywa się kolejno poszczególnymi rzędami bez wyłączenia filtra z pracy. Częstotliwość regeneracji oraz czas trwania impulsu ustawia się w szafce sterowniczej w zależności od parametrów filtracji.
Rodzaje filtrów workowych
TYP GF
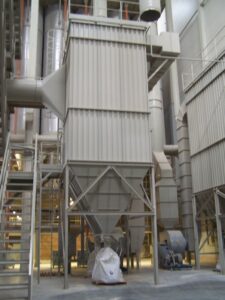
Oznaczenie filtra składa się z symbolu GF, symbolu wielkości (8×8-2 ÷ 30×8-5 – filtry jednorzędowe) oraz (12×16-2 ÷ 60×16-5 – filtry dwurzędowe). Prędkość filtracji wynosi 0,02 ÷ 0,06 m/s, maksymalna koncentracja pyłu przed filtrem to 100g/m3.
Filtry pulsacyjne typu GF są produkowane w 327 wielkościach, powierzchnia filtracyjna to od 60 m2 do 2240 m2 (filtry typu GF są projektowane indywidualnie do potrzeb klienta więc powierzchnia filtracyjna może być większa). Ilość worków w jednym rzędzie- 8 sztuk dając sumę 64 worków przy powierzchni filtracyjnej 60m2 oraz 960 worków przy powierzchni filtracyjnej 2240 m2
Filtry typu GF mają budowę modułową. Wykonane są i transportowane w elementach. Montowane są przez skręcanie śrubami i doszczelnienie połaczeń pastami, głównie silikonem. Położenie wlotu i wylotów powietrza, wysypu pyłu i doprowadzenie sprężonego powietrza mogę być zmienione o 180°C.
TYP MR
Oznaczenie filtra składa się z symbolu MR oraz symbolu wielkości
(4×7-2 ÷ 8×7-2,5).
Najczęściej stosowana prędkość filtracji wynosi 0,03 ÷ 0,04 m/s, maksymalna koncentracja pyłu przed filtrem to 50 g/m3.
Filtry pulsacyjne typu MR są produkowane w 10 wielkościach, powierzchnia filtracyjna to od 26,3 m2 do 65,5 m2 . Ilość worków w filtrze typu MR to od 28 to 56 sztuk.
TYP ZF
Oznaczenie filtra składa się z symbolu ZF oraz symbolu wielkości (101 ÷ 107; 201 ÷ 207; 301 ÷ 307; 401 ÷ 407). Powierzchnia filtracyjna filtrów typu ZF to 6,4 do 29,4 m2 przy maksymalnej liczbie 25 worków.
Filtry pulsacyjne typu ZF produkowane są w 7 wielkościach i 4 następujących wariantach:
101 ÷ 107 – komora oczyszczonego powietrza z workami i automatyką,
201 ÷ 207 – komora oczyszczonego powietrza z komorą filtracyjną i z automatyką,
301 ÷ 307 – filtr kompletny z pojemnikiem pyłu,
401 ÷ 407 – filtr kompletny z dozownikiem celkowym.
FILTROCYKLON TYPU DF
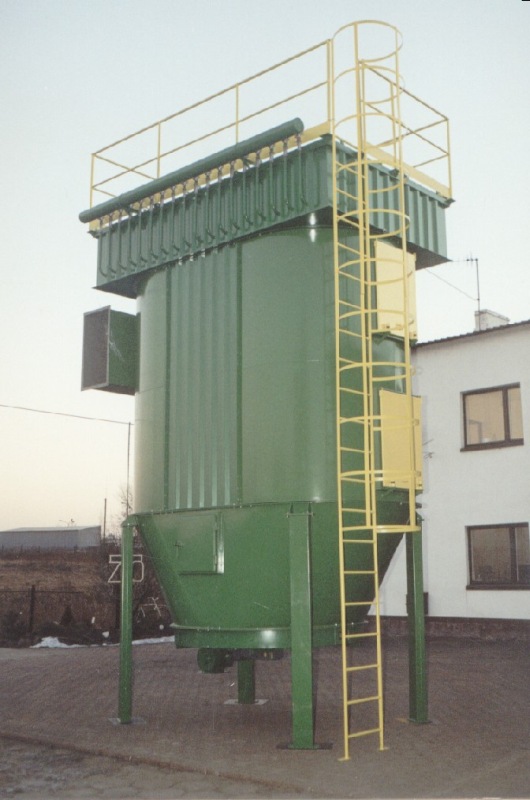
Oznaczenie filtra składa się z symbolu DF oraz symbolu wielkości (96 ÷ 276).
Filtry pulsacyjne typu DF są produkowane w 57 wielkościach i w 2 następujących wariantach:
wariant I – filtr pulsacyjny z jednym wygarniaczem obrotowym,
wariant II – filtr pulsacyjny z dwoma wygarniaczami obrotowymi.
Filtry z pojedynczym wygarniaczem obrotowym produkowane są w 4 wielkościach (96, 106, 116, 126) oraz w 3 długościach worków filtracyjnych (3010 mm, 3510 mm, 4010 mm).
Filtry z dwoma wygarniaczami obrotowymi produkowane są w 15 wielkościach (136, 146, 156, 166, 176, 186, 196, 206, 216, 226, 236, 246, 256, 266, 276) oraz w 3 długościach worków filtracyjnych (3010 mm, 3510 mm, 4010 mm)
Worki filtracyjne wymienialne są od góry filtra. tj. od strony czystej poprzez pokrywy w komorze oczyszczonego powietrza. Worki mocowane są na tzw. „snapringi”.
TYP HF
Oznaczenie filtra składa się z symbolu HF oraz symbolu wielkości (3×2-1,5 ÷ 72×6-2,5). Filtry poziome typu HF są produkowane w 200 wielkościach i w dwóch wariantach:
Wariant I – komora oczyszczonego powietrza z komorą filtracyjną i workami. Filtry takie są stosowane najczęściej na obudowach przenośników, ich przesypów oraz silosach. Standardowo wykonywany filtr jest wyposażony w wentylator promieniowy umieszczony z boku komory oczyszczonego powietrza oraz w dwa króćce wlotowe. Często wyposażone są w wentylator. Stanowią wtedy filtr stanowiskowy nie wymagający dodatkowej instalacji rurowej. Ze względu na niewielkie gabaryty są one transportowane w stanie zmontowanym w całości wraz z podłączonymi zaworami do szafki sterowniczej. W przypadku trudności z transportem na miejsce zainstalowania mogą być wykonane w elementach i skręcone na miejscu posadowienia.
Wariant II – komora oczyszczonego powietrza z komorą filtracyjną i workami, zsyp z przenośnikiem i dozownikiem celkowym. Standardowo filtry te nie posiadają konstrukcji wsporczej, przeznaczone są głównie do instalowania na stropach tak, że komora filtracyjna i komora doprowadzenia powietrza zapylonego znajdują się na górnej kondygnacji, natomiast zsyp z przenośnikiem ślimakowym i dozownikiem na kondygnacji dolnej. Indywidualnie, dla każdej wielkości filtra oraz do życzeń zamawiającego, projektuje się i wykonuje sposób odbioru pyłu i ewentualnej konstrukcji wsporczej. Filtry w tym wariancie ze względu na duże gabaryty mają budowę modułową. Wykonane są i transportowane w elementach. Montowane są przez skręcenie śrubami i doszczelnienie połączeń pastami – głównie silikonem.
Filtry w wersji izolowanej wykonywane są z izolacją termiczną w postaci wełny mineralnej o grubości 50 mm i blachy ocynkowanej. Stosowane są tam, gdzie nadmierne schłodzenie gazu odpylanego może doprowadzić do szkodliwego zjawiska kondensacji wilgoci, tzn. roszenia na ścianach filtra.
Filtry patronowe
Filtry patronowe typu FP przeznaczone są do instalowania w pomieszczeniach zamkniętych i na otwartej przestrzeni. Przeznaczone są do odpylania powietrza z pyłów suchych i nie klejących. Mogą pracować w części podciśnieniowej i nadciśnieniowej instalacji. Filtry patronowe typu FP mogą być stosowane w instalacjach odpylających w przemyśle cementowym, wapienniczym, odlewniczym, hutniczym, materiałów budowlanych, spożywczym, młynarskim, paszowym, tworzyw sztucznych, chemicznym, drzewnym, stolarskim, w instalacjach centralnego odkurzania, itp. Jeżeli odpylane gazy nie zawierają pary wodnej, filtry te mogą być instalowane na otwartej przestrzeni bez izolacji termicznej. Wkłady patronowe (patrony) wymienia się od góry tj. od strony czystej. Na życzenie zamawiającego mogą być wymieniane od wnętrza komory filtracyjnej (w tej wersji brak barierek i drabiny na górną powierzchnię filtra). Oprócz wkładów patronowych f 225 x 1000 mm o powierzchni filtracyjnej 5 m2 mogą być stosowane wkłady patronowe f 325 x 660 mm o powierzchni filtracyjnej 13 m2. Zastosowanie takich wkładów pozwala na zwiększenie maksymalnej powierzchni filtracyjnej do 520 m2. Zastosowanie wkładów patronowych f 325 x 1000 mm pozwala jeszcze bardziej zwiększyć powierzchnię filtracyjną filtra patronowego typu FP. Dla każdej instalacji odpylającej wymagany jest osobny dobór rodzaju i struktury materiału filtracyjnego (wkładu patronowego) oraz parametry filtracji i regeneracji. Dobór ten należy przeprowadzić w zależności od temperatury zapylonego powietrza, rodzaju i właściwości pyłu, zawartości pary wodnej, substancji kwasowych i zasadowych. W ofercie są różne materiały do suchego filtrowania powietrza np. papier, polipropylen, poliester, ryton. Wykonywane są z impregnacją hydrofobową, oleofobową, z powłoką antystatyczną, z membraną PTFE, z powłoką napylaną aluminium. Producent filtrów udziela porad w doborze materiału filtracyjnego (wkładów patronowych) oraz parametrów filtracji i regeneracji. W razie potrzeby filtry patronowe typu FP mogą być:
- izolowane 50 mm wełny mineralnej,
- wykonane ze stali kwasoodpornej,
- wyposażone w zabezpieczenia do odpylania gazów z pyłów wybuchowych (wykonanie zgodnie z wymaganiami ATEX),
Na życzenie zamawiającego mogą być wprowadzone dodatkowe zmiany. Czytaj więcej: Przeznaczenie filtrów patronowych Budowa i działanie filtrów patronowych Rodzaje filtrów patronowych
Filtrocyklony
Filtrocyklony typu MF przeznaczone są do instalowania w pomieszczeniach zamkniętych i na otwartej przestrzeni.
Filtrocyklony przeznaczone są do odpylania powietrza z pyłów suchych i nie klejących. Dla mieszanin pyłowo-powietrznych wybuchowych filtrocyklony wykonywane są zgodnie z wymaganiami ATEX i posiadają zabezpieczenia odpowiednie dla danego pyłu, takie jak:
- uziemienie worków filtracyjnych wykonanych z odpowiedniej włókniny elektroprzewodzącej,
- otwory dekompresyjne zamknięte klapą lub atestowaną membraną dekompresyjną.
Filtrocyklony przeznaczone są zasadniczo do pracy w części podciśnieniowej instalacji, ale mogą także pracować w części nadciśnieniowej. Jeżeli odpylane gazy nie zawierają pary wodnej, filtrocyklony te mogą być instalowane na otwartej przestrzeni bez izolacji termicznej. W przypadku ograniczeń wysokościowych oferuje się filtrocyklony z dnem płaskim wyposażone w wygarniacz obrotowy. W zależności od temperatury oczyszczanego gazu filtry wyposażone są w dysze polipropylenowe (do 60 °C) lub aluminiowe (powyżej 60 °C oraz dla wersji zgodnie z wymaganiami ATEX). Dla każdej instalacji odpylającej wymagany jest osobny dobór rodzaju i struktury włókniny filtracyjnej (filcu igłowego) oraz parametrów filtracji i regeneracji. Dobór ten należy przeprowadzić w zależności od temperatury zapylonego powietrza, rodzaju i właściwości pyłu, zawartości pary wodnej, substancji kwasowych i zasadowych. Worki mogą być wykonane z różnych rodzajów filcu igłowanego (poliester, polipropylen, Dolomit, PPS, Nomex, P-84, Teflon, itd.) i z różnymi rodzajami obróbek.
Doboru tego dokonuje inwestor lub projektant instalacji odpylającej. Producent filtrocyklonów udziela porad w doborze włókniny i parametrów filtracji i regeneracji.
Filtrocyklony typu MF mogą być stosowane w instalacjach odpylających w przemyśle cementowym, wapienniczym, odlewniczym, hutniczym, materiałów budowlanych, spożywczym, młynarskim, paszowym, tworzyw sztucznych, chemicznym, drzewnym, stolarskim, w instalacjach centralnego odkurzania itp. Czytaj więcej: Przeznaczenie filtrocyklonów Budowa i działanie filtrocyklonów Rodzaje filtrocyklonów
Filtry stanowiskowe
Filtry stanowiskowe przeznaczone są do odpylania stanowisk technologicznych, na których występuje emisja pyłów suchych i nie klejących. Są to filtry pulsacyjne w wykonaniu kompaktowym.
W wersji standardowej filtry te posiadają zamontowany średnioprężny wentylator promieniowy, włącznik wentylatora i szafkę sterowania elektrozaworami przedmuchowymi. Filtry te nie mogą być stosowane do pyłów tworzących z powietrzem mieszaniny wybuchowe, ponieważ nie posiadają zabezpieczeń przed skutkami wybuchu.
Filtry stanowiskowe mają skuteczność odpylania powyżej 99 % i mogą być stosowane do odpylania szlifierek, polerek, pakowaczek, przesypów, itp., w przemyśle materiałów budowlanych, metalowym, chemicznym, odlewniczym.
Filtry stanowiskowe typu FS z wkładami patronowymi należy stosować dla mniejszego zapylenia oraz dla pyłów łatwiej usuwanych z powierzchni wkładu filtracyjnego.
Filtry stanowiskowe typu HF oraz filtry typu FS z workami filtracyjnymi można stosować dla większego zapylenia oraz pyłów trudniej usuwanych z powierzchni worka filtracyjnego.
Filtry stanowiskowe typu FS są wyposażone we wkłady patronowe (plisowane) Ø 225 mm i długości 1000 mm o powierzchni filtracyjnej 5 m².
Filtry stanowiskowe typu FS-3×4 są wyposażone w pionowe kosze i worki filtracyjne o przekroju kołowym Ø 153 mm i długości 1550 mm i 2050 mm.
Filtry stanowiskowe typu HF są wyposażone w poziome kosze i worki filtracyjne o przekroju soczewkowym o długości1500 mm, 2000 mm i 2500 mm.
Czytaj więcej:
Przeznaczenie filtrów stanowiskowych Budowa i działanie filtrów stanowiskowych Rodzaje filtrów stanowiskowych

Odpylacze mokre
Odpylacze mokre typu OMG przeznaczone są do odpylania powietrza z pyłów mokrych lub zwilżalnych. Stanowią one drugi stopień odpylania (po filtrocyklonach). W odpylaczach mokrych strumień zapylonego gazu jest odpylany wskutek kontaktu z cieczą. Jeśli odpylacz zlokalizowany jest na zewnątrz pomieszczenia, należy wyposażyć go w instalację grzewczą (podgrzewającą wodę). Instalację taką (instalację ogrzewania wody w odpylaczu) Zamawiający wykonuje przeważnie we własnym zakresie.
Odpylacze mokre typu OMG znajdują zastosowanie w suszarniach, przemyśle ceramicznym, odlewniczym oraz w produkcji tworzyw sztucznych.
Czytaj więcej:
Przeznaczenie odpylaczy mokrych Budowa i działanie odpylaczy mokrych Rodzaje odpylaczy mokrych

Odpylanie kotłowni węglowej
Centralne odkurzanie przemysłowe
Przemysłowa instalacja centralnego odkurzania może być stosowana w zakładach przemysłowych gdzie z nieszczelnych urządzeń technologicznych i transportowych wydostają się duże ilości pyłu, który osadza się na podłogach, urządzeniach i konstrukcjach. Ze względu na małą pojemność zbiorników tradycyjnych odkurzaczy jedynym rozwiązaniem przy tak ogromnych ilościach pyłu jest przemysłowa instalacja centralnego odkurzania.
Dozowniki celkowe
Dozowniki celkowe są urządzeniami służącymi do odbioru pyłu z urządzeń odpylających i różnego rodzaju zbiorników magazynujących. Jednocześnie dozowniki spełniają funkcję szczelnego zamknięcia w/w elementów tak podczas pracy, jak i w trakcie postoju dozowników. Dzięki szczelnemu zamknięciu dozowniki zapobiegają dekompresji urządzeń, z którymi współpracują.
Przenośniki ślimakowe
Przenośniki ślimakowe są urządzeniami służącymi do transportowania pyłów z urządzeń odpylających i różnego rodzaju zbiorników magazynujących, takich jak: np. silosy, zbiorniki. Mogą transportować różne pyły od bardzo miałkich i drobnoziarnistych do ziaren o dużej granulacji. Transport pyłów może odbywać się w poziomie lub pod kątem.